Performance review
Facade design: Al-Ansar Mosque

The Al-Ansar Mosque project was completed in 2015 in collaboration with KD Architects. We recently revisited the mosque to review an aspect of the design—the façade, specifically— to examine its performance and design integrity. Through this, we hope to share the thought processes behind the design of the façade and to identify what could have been done better.
In Singapore’s tropical climate, the issue of weathering, and protection against year-round torrential rain and the harsh sun are often key considerations in the design of a building. In that same light, the design brief for the Al-Ansar Mosque façade was fairly straightforward: to have a cohesive language that identifies with the religion, and to function as a breathable skin protecting the building against weather. The façade's aesthetics took reference from geometric representations within Islam, which were then tessellated to allow for a flexibility of multiplication and enlargement where needed.
In Singapore’s tropical climate, the issue of weathering, and protection against year-round torrential rain and the harsh sun are often key considerations in the design of a building. In that same light, the design brief for the Al-Ansar Mosque façade was fairly straightforward: to have a cohesive language that identifies with the religion, and to function as a breathable skin protecting the building against weather. The façade's aesthetics took reference from geometric representations within Islam, which were then tessellated to allow for a flexibility of multiplication and enlargement where needed.
GEOMETRY OF ONE MODULE
4 FACADE MODULES
One of the challenges for the façade was to find a suitable material, lightweight yet versatile enough for design execution. Fire resistance was also a must, to comply with SCDF’s safety requirements. Aluminium, composite aluminium and some other options were tossed around. When we came across foam with Dryvit coating, we were excited by its potential. It met our conditions of being light, versatile and fire resistant, and had the bonus of being cost-efficient. The coating of Dryvit also allowed for external façade paint to be applied. And while it was not yet a common material used in local building, the clients were open to implementing the proposal.
The inner void of each façade module was tilted at an angle of 30 degrees. This prevented pigeons—the bane of all buildings in Singapore—from perching or nesting on the façade, addressing one of the client’s strongest concerns. Visually, this also accentuated the depth of the void, allowing for an interesting skewed articulation of the geometry.
To guide rainwater down the front of the façade (and the dirt that is washed along with it), drip channels were added around the side and bottom lip of the module. This was expressed as a series of 20mm x 20mm groove lines along the sides and front. To further channel the water flow, each module was tapered out at the bottom, creating an overlapping effect through shadows casted from the overhang. On the contrary, the module’s back elevation was kept vertically flat, due to the functional need to be attached to substructures. In revisiting the façade, we observed that after three years of use, streaking within the drip channels can be seen up close, while other surfaces were relatively clean.
The inner void of each façade module was tilted at an angle of 30 degrees. This prevented pigeons—the bane of all buildings in Singapore—from perching or nesting on the façade, addressing one of the client’s strongest concerns. Visually, this also accentuated the depth of the void, allowing for an interesting skewed articulation of the geometry.
To guide rainwater down the front of the façade (and the dirt that is washed along with it), drip channels were added around the side and bottom lip of the module. This was expressed as a series of 20mm x 20mm groove lines along the sides and front. To further channel the water flow, each module was tapered out at the bottom, creating an overlapping effect through shadows casted from the overhang. On the contrary, the module’s back elevation was kept vertically flat, due to the functional need to be attached to substructures. In revisiting the façade, we observed that after three years of use, streaking within the drip channels can be seen up close, while other surfaces were relatively clean.
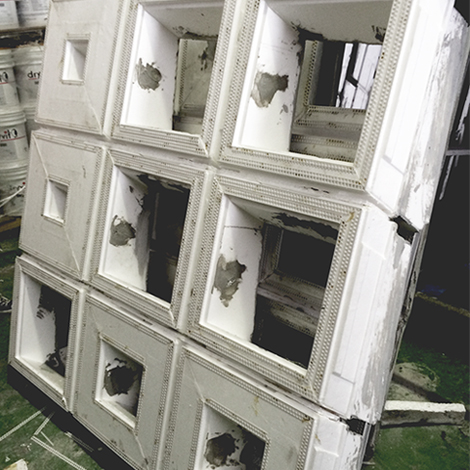
ASSEMBLING OF 9 MODULES

DRYVIT APPLICATION ON FOAM
FACADE AS A SKIN
4 VARIATION OF FOAM FACADE PANELS
We had initially developed five separate modules, but due to the production cost of creating the moulds, the design was streamlined into a set of four varying modules. Further cost implications led us to increase the module sizes from 300mm x 300mm to a larger 500mm x 500mm.
From the four finalised modules, four panels of 11 x 11 modules were created, each with varying opacity. These variations addressed the functions of spaces behind the façade. For example, a more porous panel was used where there was a need for light at communal spaces, while more opaque panels could be installed in front of solid walls.
For installation, these panels were then broken down into 1.5m x 1.5m units of 3 x 3 modules, so they could be attached to a secondary frame. Integrated galvanized mild steel joints held the modules together in their unit configuration. The whole unit was then bolted to rectangular hollow sections, placed at 1.5m from centre to centre on a diagonal. Finally, these diagonal structures were attached to the main horizontal beams, fixing the façade in place. The tight configuration hides the bulk of the main structures, so that the geometry of the modules is expressed, and also left no room for pigeons to settle on any part of the façade.
For installation, these panels were then broken down into 1.5m x 1.5m units of 3 x 3 modules, so they could be attached to a secondary frame. Integrated galvanized mild steel joints held the modules together in their unit configuration. The whole unit was then bolted to rectangular hollow sections, placed at 1.5m from centre to centre on a diagonal. Finally, these diagonal structures were attached to the main horizontal beams, fixing the façade in place. The tight configuration hides the bulk of the main structures, so that the geometry of the modules is expressed, and also left no room for pigeons to settle on any part of the façade.
PART FOAM FACADE ASSEMBLY DETAIL
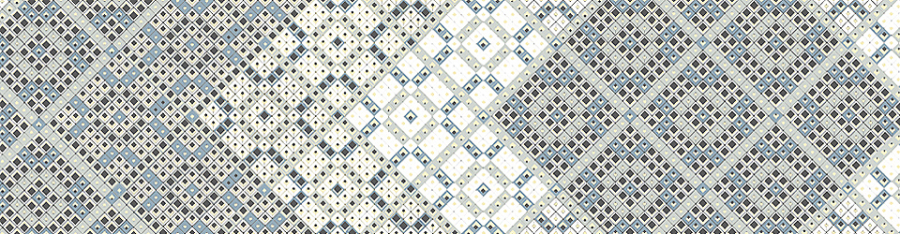
COLOUR APPLICATION
The final layer—literally and figuratively—to the façade’s overall design consideration was colour. Historically, Al-Ansar Mosque was synonymous with a prominent light blue that covered the entire building. To celebrate and continue that identity, we introduced that same blue in the façade, with a secondary accent of yellow that was applied on the inner surfaces of the modules for more depth.
CHALLENGES
One of the difficulties in approaching the façade as a skin was the resolution of corner pieces, given that the skin wraps the building at varying angles. Even though we preempted angles and turns as best as we could, site conditions and construction tolerance meant that we could not achieve complete accuracy at the planning stage. The final resolution could only be achieved by manually cutting and adjusting the modules in-situ. This proved to be very challenging, despite efforts on quality control, and was highly reliant on the skills of the workers.

3D TEST OF CORNER JOINT

MOCKUP OF CORNER MODULES
Integration of the Fire Access Panel (FAP) proved to be an interesting challenge, as we had to provide a regular opening of at least 850mm (W)x 1000mm (H) within the façade panel for firefighting purposes. The initial idea of having an opening that coincided with the geometry of the façade was rejected, and conversations with the relevant authorities were held to identify possible methods for providing the access. Modifications to the substructure were made, and concealed hinges introduced to create accessible panels on the façade.
We chose to continue the diagonal geometry by retaining an angular profile at the top of the façade, which also served as a continuation of our zero-tolerance policy towards pigeons. To cap the façade and prevent water from penetrating the joint between roof parapet walls and the façade, we designed a custom flashing that followed the jagged edges and inclination of the modules.
In retrospect, the manual process of design exploration was laborious as the façade followed various geometries and angles, and any change or permutation required tedious recalculations and re-planning. When dealing with a porous façade, in-depth daylight studies are greatly useful, in understanding user needs and checking the design for feasibility. Perhaps environmental studies with the aid of parametric tools would have helped us with performative studies into the ongoing design.
Through this project, the importance of allowing for sufficient construction tolerance also became apparent. Especially when dealing with the manual installation of precise, prefabricated modules, misalignment may occur, particularly at corner terminations. Any number of unforeseen factors can easily affect a precise system design, but can be mediated through sufficient tolerance.
Three years on, and the façade is holding up well. Signs of weathering and staining have occurred mostly at the drip channels, and there is not a single pigeon in sight. We look forward to revisiting the project again after ten years, to further study how the material and construction have held up.
We chose to continue the diagonal geometry by retaining an angular profile at the top of the façade, which also served as a continuation of our zero-tolerance policy towards pigeons. To cap the façade and prevent water from penetrating the joint between roof parapet walls and the façade, we designed a custom flashing that followed the jagged edges and inclination of the modules.
In retrospect, the manual process of design exploration was laborious as the façade followed various geometries and angles, and any change or permutation required tedious recalculations and re-planning. When dealing with a porous façade, in-depth daylight studies are greatly useful, in understanding user needs and checking the design for feasibility. Perhaps environmental studies with the aid of parametric tools would have helped us with performative studies into the ongoing design.
Through this project, the importance of allowing for sufficient construction tolerance also became apparent. Especially when dealing with the manual installation of precise, prefabricated modules, misalignment may occur, particularly at corner terminations. Any number of unforeseen factors can easily affect a precise system design, but can be mediated through sufficient tolerance.
Three years on, and the façade is holding up well. Signs of weathering and staining have occurred mostly at the drip channels, and there is not a single pigeon in sight. We look forward to revisiting the project again after ten years, to further study how the material and construction have held up.

THE FACADE
BEST WHEN TAKEN WITH A PINCH OF SALT.
PLEASE EMAIL FARMACY@FARM.SG WITH YOUR FEEDBACK, OR IN CASE OF ANY INACCURACIES.
PLEASE EMAIL FARMACY@FARM.SG WITH YOUR FEEDBACK, OR IN CASE OF ANY INACCURACIES.
REF. NO.
PROTOTYPES-001-AL-ANSAR-MOSQUE-FACADE-REVIEW
CONTRIBUTOR(S)
LEE HUI LIAN, CHEUNG YUTING
PUBLISHED
08.08.18